Choosing the Right Aluminum Machining Manufacturer
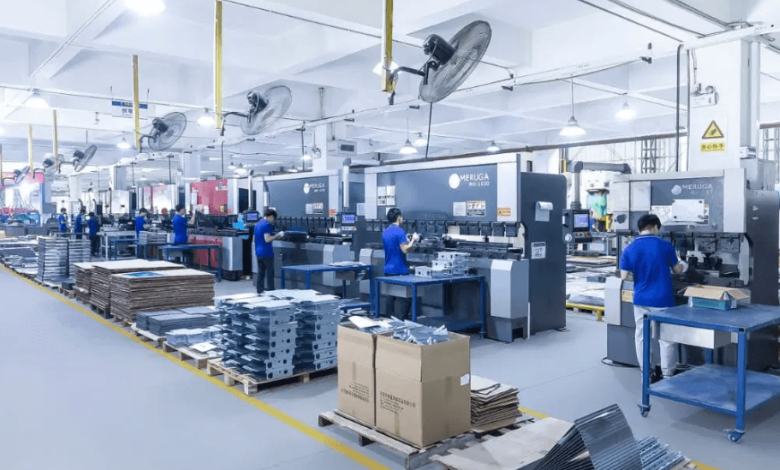
Introduction
In the evolving world of modern manufacturing, aluminum stands out as one of the most widely used materials due to its lightweight nature, excellent machinability, and corrosion resistance. As demand grows for high-precision parts in industries such as aerospace, automotive, electronics, and medical devices, the role of an expert aluminum machining manufacturer becomes increasingly vital.
This article provides a detailed exploration of what an aluminum machining manufacturer offers, the capabilities involved, quality assurance practices, and how to choose the right partner for your business needs.
What Does an Aluminum Machining Manufacturer Do?
An Aluminum Machining Manufacturer specializes in producing custom and standard aluminum components using advanced machining techniques such as CNC milling, turning, drilling, and surface finishing. These manufacturers handle everything from material selection to the final product, ensuring that each part meets the required specifications.
Unlike general-purpose machine shops, these manufacturers have specific expertise in working with aluminum grades like 6061, 7075, and 2024, optimizing processes to ensure minimal waste, precise tolerances, and superior finishes.
Key Capabilities
CNC Machining
It allows for:
- Complex geometries
- High-speed production
- Micron-level accuracy
The manufacturer programs CNC machines to cut and shape aluminum into precise forms based on CAD models.
Milling and Turning
Milling is used to create complex shapes, pockets, and contours, while turning is ideal for cylindrical components. A reliable aluminum machining manufacturer uses multi-axis equipment to reduce the number of setups and improve accuracy.
Drilling and Tapping
Manufacturers integrate automated drilling and tapping to create threads quickly and with excellent repeatability.
Finishing Services
Surface treatment not only improves the appearance of parts but also enhances their durability. Finishing services may include:
- Anodizing: For corrosion resistance and coloring
- Powder coating: For aesthetic and environmental protection
- Bead blasting: For a smooth, matte surface
- Polishing: For decorative or reflective parts
Why Aluminum?
Lightweight: Reduces product weight without compromising strength
- Corrosion-resistant: Especially important for outdoor or marine applications
- Easy to machine: Faster cycle times and reduced tool wear
- Recyclable: Environmentally sustainable
These properties make aluminum ideal for industries where performance, aesthetics, and sustainability matter.
See also: Affordable Small Business Health Insurance A Complete Guide
Applications Across Industries
Aerospace
Aerospace components demand extreme precision and must be lightweight without sacrificing strength. Aluminum parts are used in structural frames, instrumentation, and housing units.
Automotive
Medical Devices
Surgical tools, diagnostic equipment, and prosthetic parts often rely on aluminum for its biocompatibility and lightweight nature. These components must adhere to tight tolerances and medical-grade finishing.
Electronics
Aluminum’s excellent thermal conductivity makes it ideal for electronic housings, heat sinks, and enclosures. The material dissipates heat efficiently, protecting sensitive components.
Industrial Equipment
Machine parts, brackets, supports, and connectors used in heavy-duty applications often rely on aluminum machining for both functionality and durability.
Technology Integration
A professional aluminum machining manufacturer doesn’t just offer machining services—they integrate cutting-edge technologies to streamline production. These include:
- CAD/CAM software for precision programming
- ERP systems for managing inventory, scheduling, and logistics
- IoT-enabled machines for real-time monitoring and maintenance alerts
The integration of such technologies ensures that production is not only efficient but also adaptable to customer-specific needs.
Quality Control and Assurance
Precision and consistency are critical in aluminum machining. To ensure high standards, manufacturers invest in robust quality assurance systems. These include:
- In-process inspections
- Final part verification using CMM (Coordinate Measuring Machines)
- Material certifications and traceability
By prioritizing quality, the manufacturer ensures that each part meets design tolerances and functional requirements.
Factors to Consider When Selecting a Manufacturer
Choosing the right aluminum machining manufacturer can significantly impact your product’s performance, cost, and lead time. Here are key factors to consider:
Experience
Look for manufacturers with proven experience in aluminum machining, especially in your specific industry. Years of expertise translate to better understanding of materials, tolerances, and finishing techniques.
Equipment
Modern machinery ensures precision, speed, and the ability to handle complex geometries. Ask about the types of machines used, their capacity, and how often they’re calibrated or maintained.
Customization
The ability to handle custom projects with unique specifications is essential. A good manufacturer offers engineering support, design-for-manufacturing (DFM) consultations, and flexible production volumes.
Turnaround Time
Efficient scheduling and a streamlined workflow reduce lead times. Inquire about typical delivery windows and whether they can accommodate rush orders when necessary.
Certifications
Certifications are an assurance of quality and compliance. ISO, RoHS, and ITAR certifications are indicators that the manufacturer adheres to global standards.
Communication and Support
Timely communication, design feedback, and after-sales support are indicators of a professional operation. Transparency in cost, scheduling, and project status builds long-term partnerships.
Global vs. Local Manufacturers
Depending on your business needs, you might consider sourcing from a local or international aluminum machining manufacturer.
Local Benefits
- Easier communication and time zone alignment
- Faster shipping
- Site visits and audits
Conclusion
An experienced aluminum machining manufacturer plays a vital role in delivering high-quality, precision-engineered parts for a wide range of industries. With state-of-the-art equipment, skilled technicians, and robust quality systems, these manufacturers help businesses achieve efficiency, reliability, and innovation.
Choosing the right partner involves more than just comparing prices—it means evaluating experience, capabilities, certifications, and customer service. As industries demand higher performance from their components, the value of a trusted aluminum machining manufacturer cannot be overstated.