Automotive Electronics: PCB Design Considerations
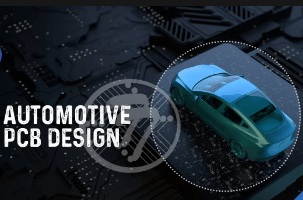
In the rapidly evolving landscape of automotive electronics, designing reliable and high-performance printed circuit boards (PCBs) has become a paramount concern. As vehicles incorporate an increasing number of semiconductor systems and hardware solutions, the demand for robust PCB development has skyrocketed. Automotive electronics are subjected to harsh environmental conditions, including extreme temperatures, vibrations, and electromagnetic interference (EMI), making their design a complex and challenging endeavour.
At the heart of automotive electronics lies the semiconductor systems integrator, responsible for seamlessly combining various components onto a PCB. This intricate process demands adherence to stringent industry standards and rigorous testing protocols to ensure safety, reliability, and optimal performance. In this article, we will delve into the critical requirements and considerations that shape PCB design for automotive electronics.
Automotive Safety Standards and Regulations
Automotive electronics are subject to a plethora of safety standards and regulations that govern their design, manufacturing, and testing processes. These standards are implemented to ensure the utmost safety of drivers, passengers, and pedestrians. Some of the key standards and regulations that PCB designers must comply with include:
- ISO 26262: Functional Safety for Road Vehicles
- IATF 16949: Quality Management System for Automotive Production
- AEC-Q100: Stress Test Qualification for Automotive Grade Integrated Circuits
- JEDEC: Standards for Semiconductor Devices and Systems
Adherence to these standards is crucial as they define the requirements for functional safety, quality management, component qualification, and various other aspects of automotive electronics design.
Environmental Considerations
Automotive electronics are exposed to a wide range of environmental conditions, from extreme temperatures to vibrations and shock. PCB designers must account for these factors to ensure reliable operation and longevity of the hardware solutions. Some key environmental considerations include:
- Temperature Ranges: Automotive PCBs must withstand temperatures ranging from -40°C to +125°C or higher, depending on the application.
- Vibration and Shock Resistance: PCBs must be designed to withstand the vibrations and shocks associated with vehicle movement, particularly in off-road conditions.
- Moisture and Humidity Resistance: Exposure to moisture and humidity can lead to corrosion and electrical failures, necessitating the use of conformal coatings and proper sealing methods.
- EMI/EMC Compliance: Automotive electronics must be shielded from electromagnetic interference (EMI) and comply with electromagnetic compatibility (EMC) regulations to prevent unintended interactions with other electronic systems.s
Careful component selection, PCB material choices, and layout techniques are employed to mitigate the effects of these environmental factors and ensure reliable operation throughout the vehicle’s lifespan.
Power Management and Efficiency
Automotive electronics often rely on multiple power sources, including batteries, alternators, and even regenerative braking systems. Effective power management is crucial to optimize energy efficiency, reduce heat dissipation, and prolong battery life. PCB designers must consider the following aspects:
- Power Distribution Networks: Robust power distribution networks must be designed to handle varying load conditions and minimize voltage drops and noise.
- Power Conversion and Regulation: Efficient power conversion and regulation circuits are essential to ensure stable and clean power delivery to various components.
- Power Budgeting and Optimization: Careful power budgeting and optimization techniques, such as low-power design and dynamic power management, can significantly improve overall system efficiency.
By addressing power management challenges, PCB designers can contribute to improved fuel efficiency, extended range for electric vehicles, and reduced environmental impact.
Thermal Management
Automotive electronics generate significant amounts of heat, which can lead to performance degradation, reliability issues, and even component failure if not properly managed. Effective thermal management is a critical aspect of PCB design for automotive applications. Techniques employed include:
- Thermal Modelling and Simulation: Computational fluid dynamics (CFD) and thermal simulations are used to predict and analyse heat dissipation patterns, enabling optimized heat sink and cooling system designs.
- Heat Sink Integration: Efficient heat sinks, either integrated into the PCB or external, are essential for dissipating heat from high-power components.
- Thermal Interface Materials: Proper selection and application of thermal interface materials, such as thermal pads or thermal greases, ensure effective heat transfer from components to heat sinks.
- Airflow and Cooling System Design: Careful consideration of airflow patterns, fan placement, and cooling system design can significantly improve thermal management in automotive electronics.
Effective thermal management not only enhances system reliability and longevity but also contributes to improved fuel efficiency and reduced emissions.
Signal Integrity and EMC
In the intricate world of automotive electronics, signal integrity and electromagnetic compatibility (EMC) are critical factors that must be carefully addressed during PCB design. High-speed digital signals, sensitive analogue signals, and power signals coexist within the same system, making signal integrity a paramount concern. Factors such as crosstalk, reflections, and ground bounce can significantly impact signal quality and system performance.
EMC, on the other hand, ensures that the electronic systems within the vehicle do not interfere with each other or with external systems, such as radio communications or navigation systems. PCB designers must employ various techniques to mitigate EMI and ensure EMC compliance, including:
- Careful trace routing and signal layer stack up.
- Proper grounding and shielding strategies
- Filtering and suppression of noise and transients
- Component placement and spacing optimization
- Adherence to industry standards and regulations (e.g., CISPR 25, ISO 11452)
By addressing signal integrity and EMC challenges, PCB designers can ensure reliable data transmission, minimize electromagnetic interference, and enhance the overall performance and safety of automotive electronics.
Design for Manufacturing and Testing
PCB design for automotive electronics must also consider manufacturability and testability aspects. These factors play a crucial role in ensuring high-quality products, efficient production processes, and cost-effectiveness. Some key considerations include:
- Design for Manufacturability (DFM): Adhering to DFM guidelines, such as component placement rules, routing constraints, and manufacturing process limitations, ensures efficient and reliable production.
- Design for Testability (DFT): Incorporating testability features, such as test points, boundary scan capabilities, and built-in self-test (BIST) circuits, enables effective testing and debugging during manufacturing and field service.
- Component Availability and Obsolescence Management: Selecting readily available components and implementing proactive obsolescence management strategies can mitigate supply chain disruptions and ensure long-term product support.
By addressing these factors, PCB designers can streamline manufacturing processes, reduce production costs, and facilitate effective testing and maintenance of automotive electronics.
See also: Increasing Workplace Efficiency with Controlio Employee Monitoring Software
Conclusion
PCB design for automotive electronics is a multifaceted discipline that requires a deep understanding of industry standards, environmental considerations, power management, thermal management, signal integrity, and manufacturing constraints. By adhering to these critical requirements and employing best practices, PCB designers can create robust and reliable hardware solutions that meet the demanding needs of the automotive industry.
As the semiconductor systems integrator for automotive electronics, PCB designers play a pivotal role in enabling the seamless integration of various components and ensuring optimal system performance. Through continuous innovation, collaboration with industry partners, and adherence to rigorous standards, the PCB development process will continue to evolve, paving the way for safer, more efficient, and more technologically advanced vehicles.